- The experts' corner
MSL levels, delamination, the popcorn effect...
What steps should be taken?
Physical constraints
The reflow temperatures of lead-free alloys are 20-30°C higher than leaded alloys. “Hermetic” components (metal or ceramic casing), pose no problem, but components with “plastic” housing present risks.
Component manufacturers have therefore had to adapt their resins to make them compatible with these temperatures without eliminating the possibility of degradation during reflow.
The main issue is the resin’propensity to absorb water vapour. During the reflow oven process, the increased temperature will cause this vapour to expand at such a rate that it cannot escape through the resin. This results in high internal pressures and therefore mechanical stresses which lead to deformations such as delamination, cracking and the popcorn effect. The latter is the most visible: the overpressure causes the component to swell and can even lead to it bursting. The internal damage is significant, electrical connections are in most cases broken and the defect will be detected either during an external visual inspection or during the board’s electrical tests. If a crack’s appearance has allowed the overpressure to escape, only a thorough external visual inspection will be able to detect that. Furthermore, while the component’s internal damage is not so great as to generate an electrical fault, the component is weakened and will be less able to withstand mechanical and environmental stresses, and its reliability will be greatly reduced.
Delamination is more pernicious as it is invisible from the outside. In the first case, it can lead to a cavity where water vapour can condense and eventually oxidise the chip’s surface, and in the second case, it can lead to mechanical fragility which, if located in the bonding area, can lead to the bondings coming off following thermal cycling. Beware, delamination is not systematically considered a component defect, the manufacturer may have performed the necessary tests to demonstrate that it has no impact on reliability.
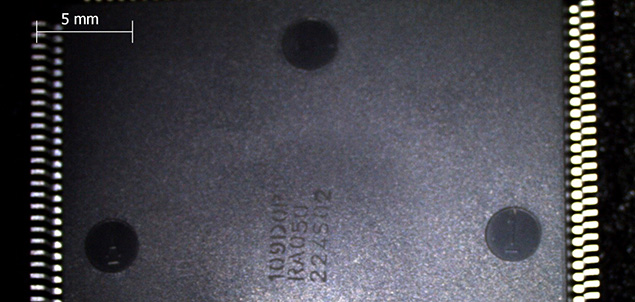
Handling precautions
Two approaches are possible:
Before remelting, the components must be cleaned of any water vapour that may have been absorbed by their resin.
First approach: dry the components before reflowing. In some cases (MSL6) this is the only solution. The J-STD-033 standard indicates what drying time is required for each MSL level depending on the temperature and the component’s thickness. However, this approach has two disadvantages: the first is that the addition of the drying operation increases the boards’ manufacturing cycle time, which will take 1 to 2 days at 125°C depending on the case type, but in the case of coils that cannot withstand this temperature, will take an enormous 79 days at 40°C! The second disadvantage is that drying exposes the component to a high temperature, which promotes oxidation of its terminations and therefore impairs its solderability.
The second approach is to prevent the component from absorbing moisture which is where the Dry-Pack comes in. The components are dried by their manufacturer before being placed in the Dry-Pack, and if the components are not exposed to moisture for too long before reflow, they can then be reflowed without having to go through the drying. This exposure time is cumulative, the maximum duration (Floor Life) depends on the MSL level (from 1 year for MSL2 to 24 hours for MSL5a). Should that time be exceeded, the parts must be dried again before remelting or re-drying.
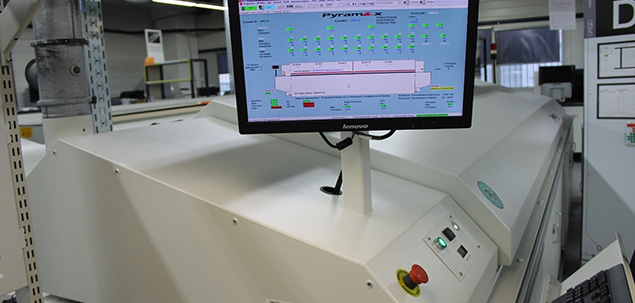
Day-to-day management
Rather than having to dry the component, it is generally preferable that the component does not absorb any moisture in the first place. However, the Dry-Pack management is a constraint for small and medium series for which the components are not used before the end of the Floor Life. It is necessary to keep track of the cumulative opening times of the bags, and also to ensure that the humidity indicator (HIC) is still valid each time the bag is opened, ensuring that no defects have occurred during the last closing of the bag, making it non-hermetic.
Managing the desiccant is vital too. The desiccant absorbs the water vapour that passes through the Dry-Pack by porosity. The quantity of desiccant is calculated in “Dose” according to the desired storage time before changing, the surface of the Dry-Pack and the humidity of the storage place.
This management, as well as the number of openings and closings of the Dry-Pack can be very demanding if you have several thousand references to manage, you can always store the components in dry cabinets, dryers or cabinets under nitrogen to avoid any return of humidity.
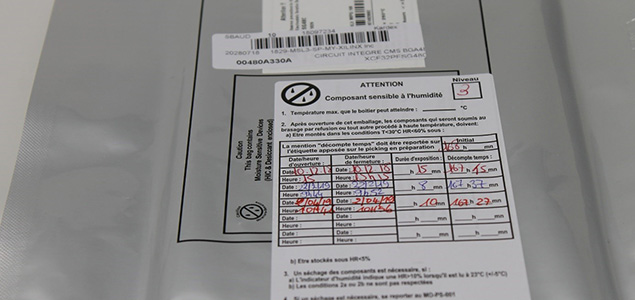
Contact
Offers tailored to the different stages of your project
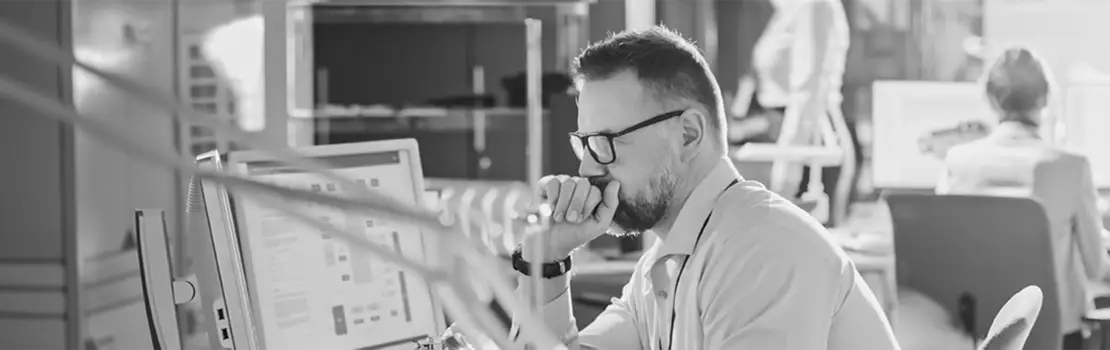
DevSolutions
Electronic product design consulting
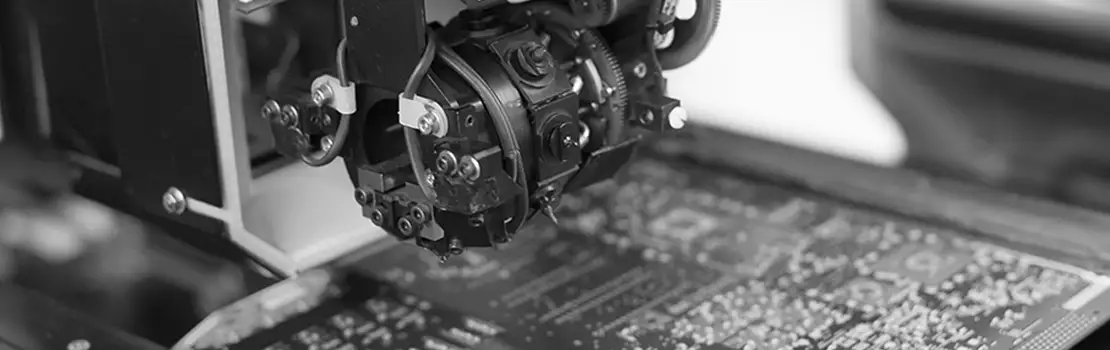
FabSolutions
Electronic component quality control
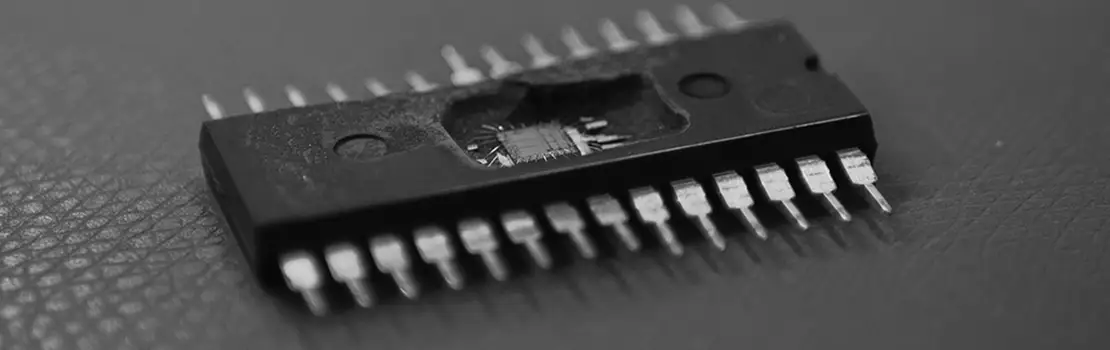
ObSolutions
Electronic component obsolescence – Advice and strategic choices