- The experts' corner
Counterfeit detection
The risks associated with outsourcing
Origin of parts, what is counterfeiting?
Counterfeiting itself is not the only fraud affecting grey market batches. Few parts have a different chip from the one expected, and even fewer are simply copied. Among the batches of rejected components, the following can be found
- components already in use ;
- components that have been scrapped during manufacture;
- genuine counterfeits.
It is possible to detect each of those frauds, but not with the same type of test. Therefore, a single test cannot ensure whether the batch is fraudulent or not. Several standards have been established to determine test flows, but also almost all major contractors have specified their own procedure. For the others, we have opted for 3 procedures (two of which are carried out under COFRAC accreditation), each with a different level of residual risk, but also a different cost to suit all possible applications of the component.
Risks, what can be done about them?
The worst thing that can happen with a fraudulent component is that it works!
If a fraudulent component doesn’t work, a defect is detected and the product is blocked.
An analysis of the board or system should then be carried out, which will pinpoint the faulty part on the component. A test on the component will identify the anomaly and indicate the fraudulent origin of the parts. There is no need to go back to the manufacturer, as few of them support the analysis of components from unauthorised sources. The best solution is to find replacement parts for the entire batch.
However, should the functional tests of the board or the system fail to reveal any defects, who knows when the failure will occur: during a stress on an untested configuration? After thermomechanical stresses? Never? It is impossible to say. The same analysis as before will detect the same fraud, only the costs associated with the analysis and replacement will be multiplied, not to mention the impact on a company’s brand image.
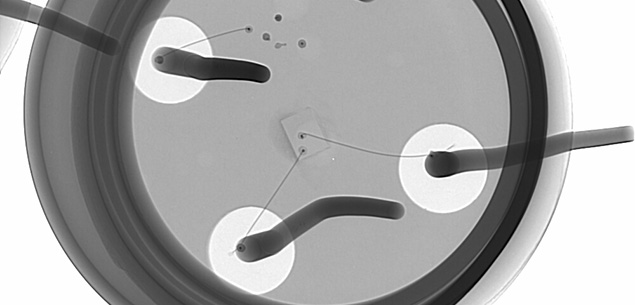
Tests, based on non-detection of evidence of fraud
The tests performed are not completely exhaustive. Whatever the procedure used, they are based on the absence of evidence of fraud, or rather on the non-detection of evidence of fraud. The further one looks without finding evidence, the lower the risk of being confronted with fraudulent material. Until, finally, it is felt that either the component is good, or it is good enough to work in the application. However, there are tests that are common to all procedures:
- External visual inspection (absence of oxidation, sanding, marking, camouflage, etc.)
- X-rays (homogeneity of the assembly, presence of the chip, bondings…)
- Electrical tests (parametric tests, functional tests, etc.)
- Destructive testing (opening, chip marking, solderability, etc.)
From one procedure to another, the depth of the tests may vary, as may the number of samples. Other analyses can also be added, such as determining the legs’ alloy finish, that the packaging hasn’t been tampered with… procedure followed often depend on what cases of fraud has previously been encountered.
Although visual inspection and X-rays can detect more than 70% of counterfeit cases, destructive and electrical tests are still necessary for the remaining 30%. But one should never lose sight of the fact that, even when dealing with new components, they weren’t manufactured yesterday.

Contact
Offers tailored to the different stages of your project
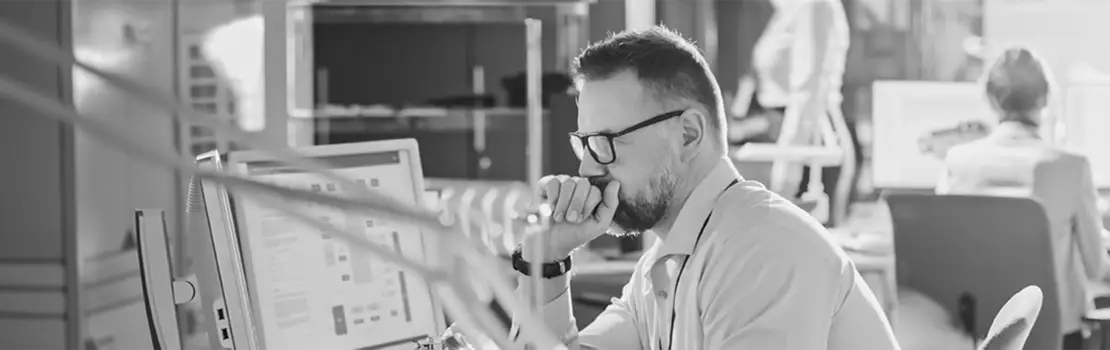
DevSolutions
Electronic product design consulting
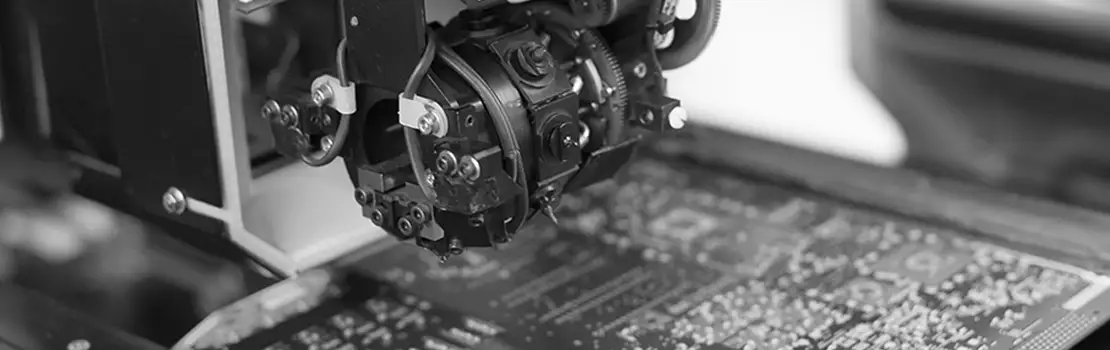
FabSolutions
Electronic component quality control
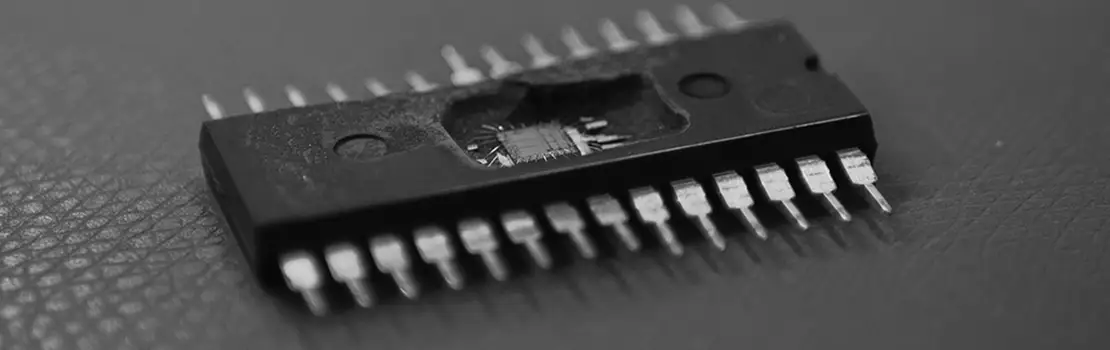
ObSolutions
Electronic component obsolescence – Advice and strategic choices