- The experts' corner
Electronic components obsolescence
How to minimise the impact of obscelence?
How does a component become obsolete?
It is estimated that 90% of electronic components are used by consumer electronics, particularly laptops, tablets and the like, and 9% by the automotive industry. The remaining percentage is used in professional electronics.
Those percentages give you an idea of your leverage when it comes to component manufacturers.
Furthermore, the manufacturers of electronic components share the same goals as you, i.e., they want to keep their customers happy, particularly through innovation. However, in doing so, this has spelled the end of many of the old products that you have long relied on.
Since the 1995 Perry Amendment in the United States, military components have gradually disappeared, which has accentuated the phenomenon. Component manufacturers no longer have an interest in keeping components available for decades for just modest quantities.
The evolution of regulations concerning hazardous materials (REACH and RoHS) has also sped up the process. Though some applications fall outside the scope of the directives, it is impossible to find components that predate them.
In most cases, manufacturers give six months prior warning before components are made obsolete and this is done by way of a PDN (Product Discontinuance Notice) or EOL (End Of Life).
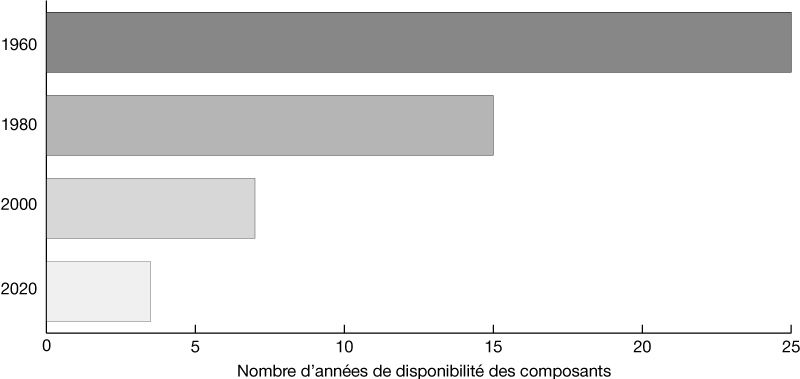
What can be done in the case of obsolescence?
There are many solutions in the case of obsolescence: use of an equivalent, purchase of stock, mezzanine, local or global redesign, broker purchase, etc.
Those solutions must be considered in accordance with the requirements such as: current production, maintenance only, product being revised, number of products affected, number of obsolete components on the product, requalification cost, ownership cost, potential new markets, etc.
There’s no one-fit solution and finding the right answer involves a diverse range of skills. The problem can’t just be left to the buyers since the decision always involves several different departments (purchasing, sales, technical, quality, etc.) It is advisable to set up a committee of some form on which all parties are represented.
The earlier the obsolescence is detected, the less likely the solution is a panicked response, and the better the risk/cost ratio. Ideally, the solution should be considered before obsolescence is declared and, above all, a budget should already be allocated to it.
There are two processes that can be put in place. The first is a passive process, leaving it to manufacturers and distributors to inform the buyers of their products of obsolescence. Beware in this first process: in most cases, distributors only commit to transmitting information on references ordered less than 2 years ago, which excludes components with a high MOQ and low usage, and second-source components which are almost never ordered. The other process is active: it consists of regular querying of obsolescence databases and component manufacturers.
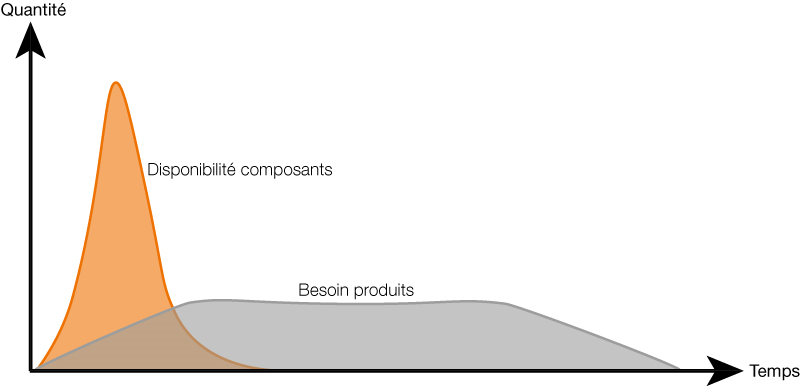
Help, it's too late! What can be done?
Everyone is eventually confronted with a lack of components on the official market, though the reasons for that lack are varied (unidentified, unprocessed, unissued or point-blank obsolescence notice, etc.)
Fast solutions, i.e. those that do not involve redesign, are becoming more limited. However, there are still a few options available:
- Replacing the component with an equivalent FFF (Form, Fit, Function). Depending on the importance of the component in the design, a partial re-qualification may be necessary. One also needs to be aware of the replacement component’s obsolescence forecast.
- Adapting a different case component in the form of a mezzanine: the new component or a set of several components are assembled on a small PCB which is itself assembled on the original board. The precautions to be taken are the same as for the above solution.
- Purchasing outsourced components. In this case, tests should be carried out to detect counterfeit components, manufacturing rejects, components already in use, etc.
- Recovery of components from old cards (unsold products, after-sales returns, etc.). Requires the development of an experimental plan to ensure that the stresses undergone by the components during the various re-melting phases (including their initial assembly, which may be decades old) are acceptable in terms of their reliability.
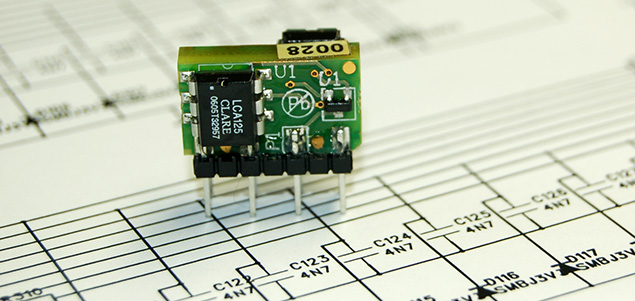
Contact
Offers tailored to the different stages of your project
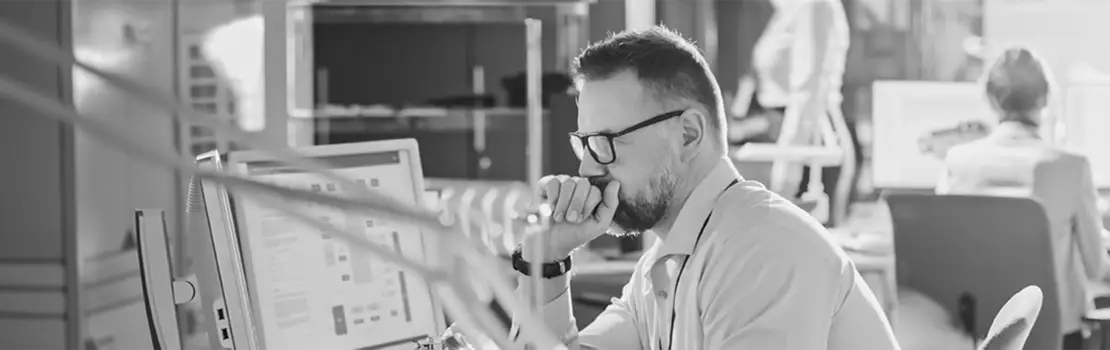
DevSolutions
Electronic product design consulting
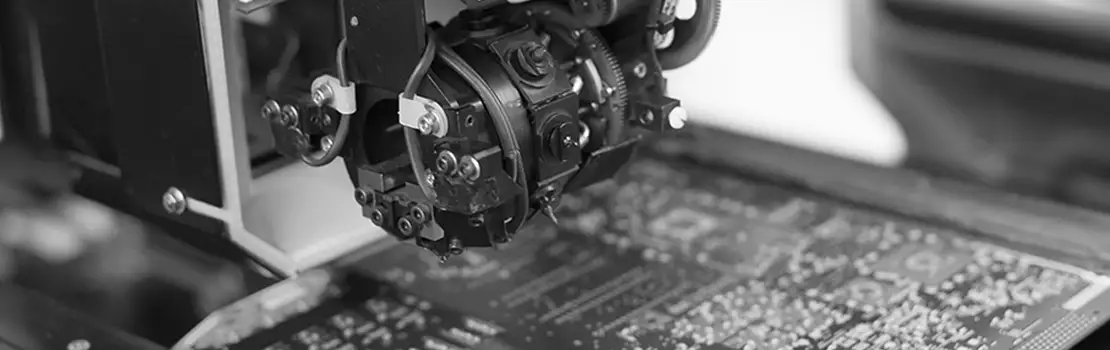
FabSolutions
Electronic component quality control
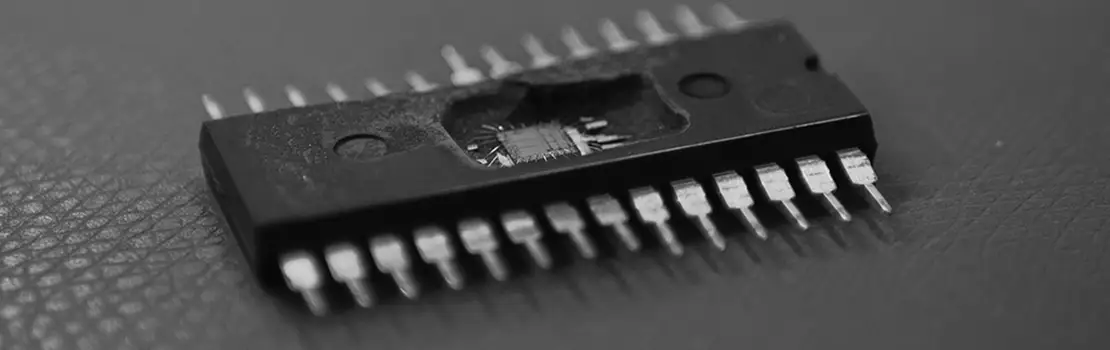
ObSolutions
Electronic component obsolescence – Advice and strategic choices