- The experts' corner
Re-tinning / RoHS
Key points for re-tinning of electronic components
Re-tinning constraints
Lead components can now only be used in exempted activities, and the number of those exempted activities is growing increasingly smaller. As a result, electronic component manufacturers are removing those lead components from their catalogues. However, the reduction of lead components is posing problems for reliability since solders containing less than 3% lead can potentially cause whiskers.
With the advent of lead-free components and processes, two procedures have been developed: FORWARD (using lead-free alloys with a lead finish component) and BACKWARD (using lead alloys with a lead-free finish component).
The first procedure often concerns RoHS products, making it necessary to ensure that the component finish’s lead content is compatible with the directive, which is often the case. The component must also be able to withstand the temperatures of a lead-free process (forward compatibility).
For the second process, it is import to ensure that the solder is homogeneous and that the finish of the component is correctly remelted.

Benefits of re-tinning the component
The main benefit of re-tinning in the forward process is a reduction of the quantity of lead in the component. The component’s legs are consecutively immersed in two pure tin baths; the first for cleaning, the second for tinning. This process dilutes the lead (though it does not entirely disappear) to less than 1% in the finish, which, given the component’s mass, will result in an overall lead content of less than 0.1%.
For the backward process, lead is added to the componet’s finish to deter whisker formation. The immersion of the component’s legs in the two baths adds lead to the component resulting in a final lead percentage of between 20 and 35%. The entire leg of the component must be covered with lead in order for the process to be effective against whiskers, leaving no areas of pure tin. Given the molten alloy’s proximity to the component’s body, care must be taken to ensure that the operation does not create any stress on the component which would be likely to affect its reliability.
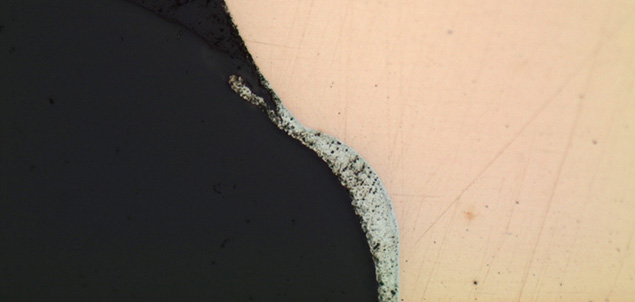
Re-tinning checks
All processes are subject to checks. Products are first checked prior to a series re-tinning, to ensure that the component is not stressed and that the re-tinning will be successful. The operation is then carried out on a sample and we check:
- to make sure there is no delamination or for plastic components, only acceptable delamination (by acoustic microscopy),
- the intermetallics created during the operation (by microsection and inspection by optical and/or electronic microscope),
- the lead content of finishes (by X-ray fluorescence),
- the solderability of the component (wetting balance).
In the production phase, the components are visually checked under binocular microscope to verify the absence of bridges between the legs, microbeads and flux residue. Tinning baths are regularly checked for pollutant concentration and have their temperature verified.
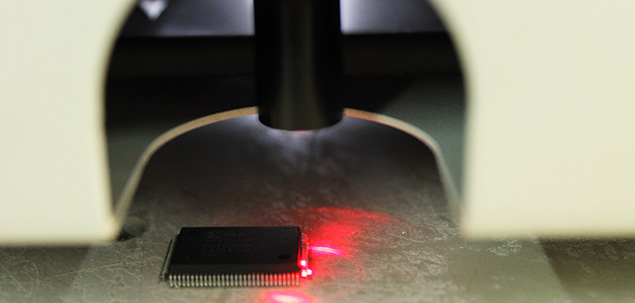
Contact
Offers tailored to the different stages of your project
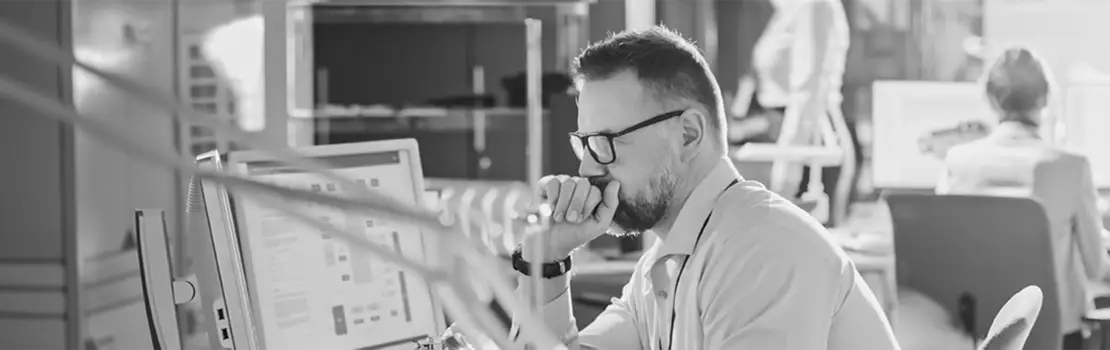
DevSolutions
Electronic product design consulting
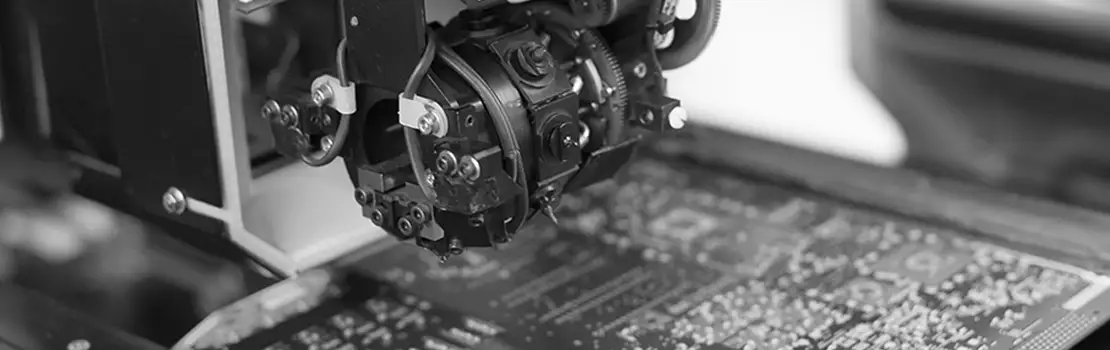
FabSolutions
Electronic component quality control
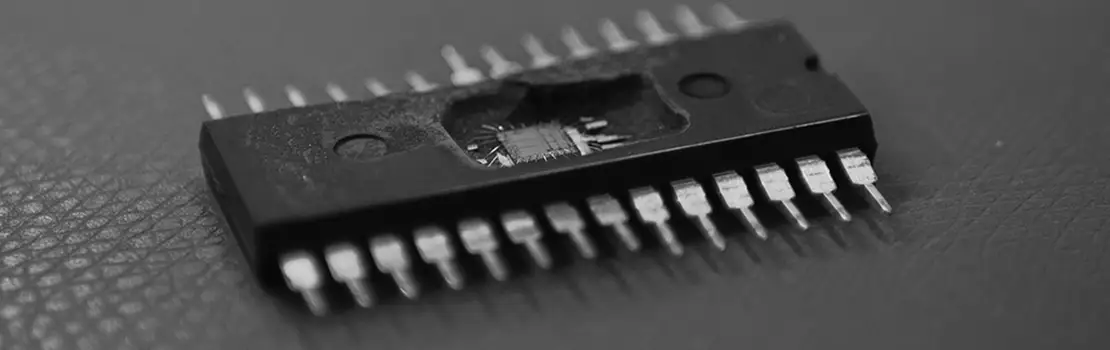
ObSolutions
Electronic component obsolescence – Advice and strategic choices