- The experts' corner
Reuse of electronic components
Palliative solutions
A new supply source
There are many possible routes for recovering missing ASIC that is impossible to remanufacture or redesign at a reasonable cost and within a reasonable timeframe. Possibilities include: after-sales returns, standard board exchanges, equipment trade-ins, unsold products…
Very often, these sources have depreciated, or are no longer valued at all, making it possible to save the unforeseen project for which the component is essential. The user already has the components he needs at home, with all their traceability, it is “simply” a matter of recovering them to be able to reuse them.
But while simple in theory, it must be understood that component manufacturers offer no guarantee of use after 3 re-melting cycles. A recovered component will undergo at least 2 more cycles, one during desoldering, the others during re-soldering. Given that the worst stress the component experiences is during the reflow phase, it is normal to question the legitimacy of the process. This is why each component reference and each board is subject to an experimental plan to determine the best desoldering tool (breakdowns, hot air, etc.) and to optimise the parameters.
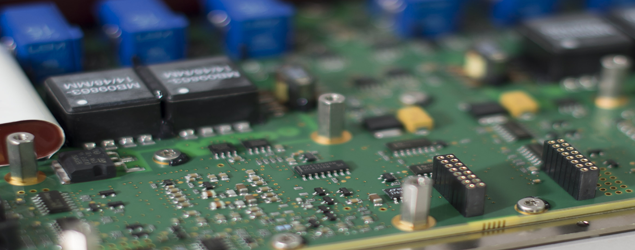
An experimental plan
The desoldering of components is not immediate. When the boards are received, they are sometimes cut, to keep only the area of interest, dried, and then put in a drypack to await desoldering. Card support tools are made to ensure that the cards are held in place during desoldering.
The cards are then placed in an oven to limit thermal shock, and then the desoldering operation can begin.
The component and its legs are then cleaned. All these operations must be carried out with great care.
To allow for this procedure to take place in the best possible circumstances, the experimental plan permits all the parameters of the profiles, temperatures, durations and means to be fixed, checking at each stage by acoustic microscopy that the component’s delamination remains at an acceptable level. The experimental design also allows the state of the components to be checked after reflow simulations, or even after thermal and/or hygrometric stress.
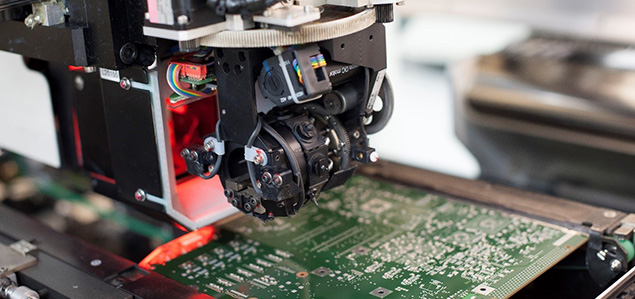
Testing and traceability
The components recovered in this way are not yet ready for use. They will require electrical tests to ensure that they are working properly, since they are not guaranteed by their manufacturer. Especially since, if they come from cards returned from after-sales service, it is possible that they have been the cause of the failure.
In the interests of advanced traceability, it is possible to associate a serial number with each component, in order to be able to make the link between a component and the results of the electrical tests at any given time. This link is made by means of a label with a Datamatrix code that can be read online during manufacture to associate the serial number of the component with the serial number of the card.
Other tests may be performed, depending on the results of the experimental design: for example, electrical tests may be conducted at temperature, or parts may be sorted by acoustic microscopy, as not all components have always been assembled with the necessary precautions on boards that may have been manufactured some fifteen years ago or more.
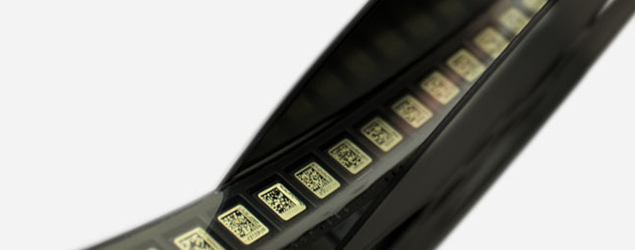
Contact
Offers tailored to the different stages of your project
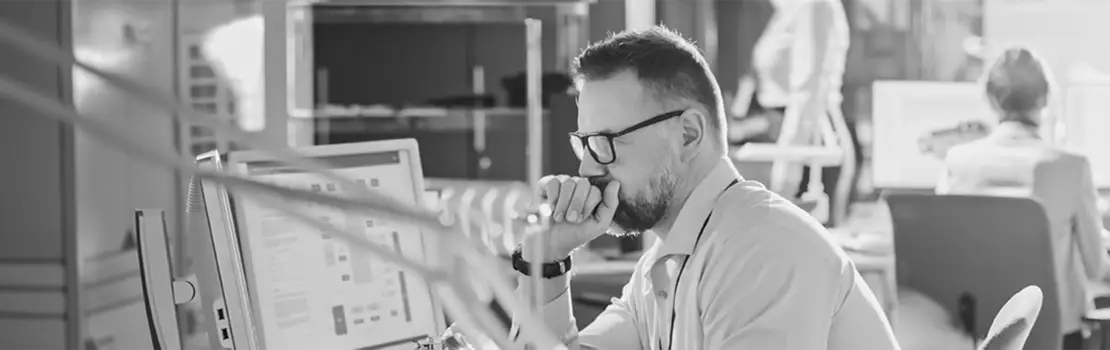
DevSolutions
Electronic product design consulting
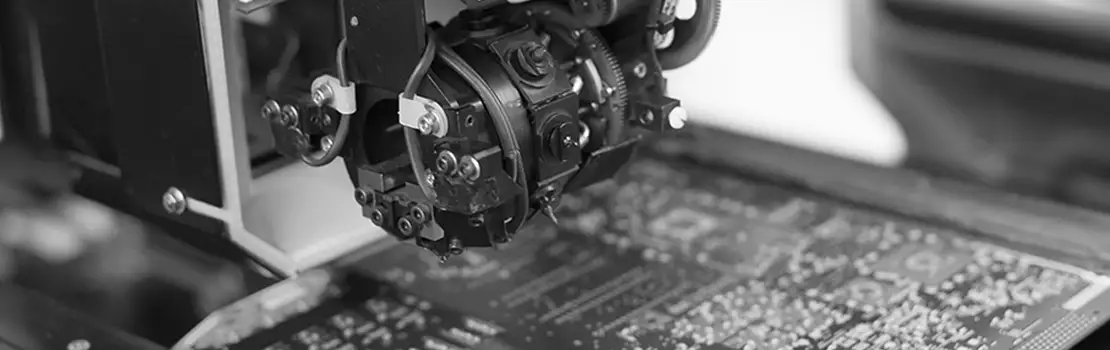
FabSolutions
Electronic component quality control
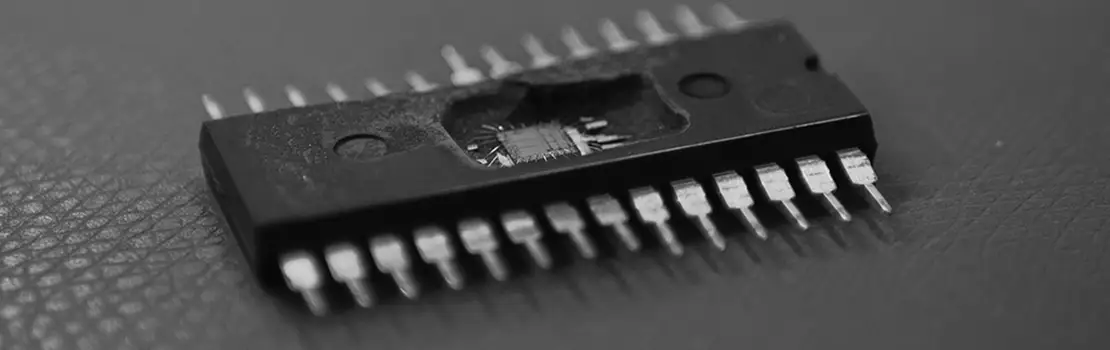
ObSolutions
Electronic component obsolescence – Advice and strategic choices