- The experts' corner
Secure storage
Issues and methods
Storage conditions
The conditions of storage should limit the degradation of the component.
The risk analysis will focus on the manufacturing quality of the components, environmental conditions, theft, limited handling, seismic and flood risks, intrinsic degradation, fire, explosion, etc. That range of potential hasards can be classified into three main categories: the component, the location, and people. Except in special cases, we store :
- In a nitrogen box: wafers, chips, semiconductor components.
- In a drypack: electronic cards.
- In shelving: finished equipment, cables, and components that cannot withstand a too dry atmosphere.
The majority of electronic components do not pose a problem for storage, but special attention should be paid to electromechanical components and components with embedded chemistry. Generally speaking, it is preferable to contact the manufacturer for these types of components:
- Relays, for example, are sealed with a resin that may not withstand a dry atmosphere; storage on shelves is preferable.
- A chemical capacitor must be recharged regularly in a controlled manner.
- A battery cannot be stored for a long period of time, unless guaranteed for such by the manufacturer.
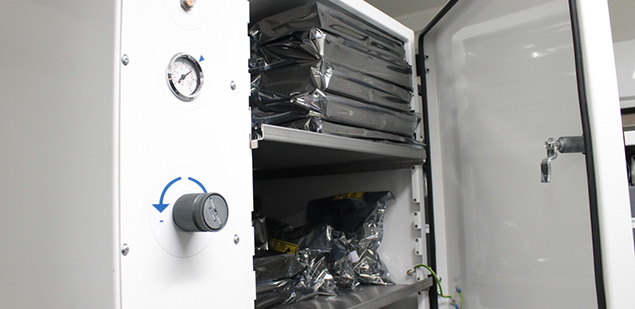
Component testing, test and be sure before placing components in stock
Even when components are sourced from authorised sources, testing them before they are placed in stock allows the manufacturer to be contacted in the event that a fault is detected. The tests are based on the UTE C96-029 guide. This guide describes the storage conditions, but also the tests to be carried out before putting components in stock as well as the periodic tests necessary according to the component and its technology.
Among the type of anomalies observed, we may find chip revisions different from that expected, delaminations in critical areas of plastic cases, different leg finishes from those expected…
However, the purpose of these tests is different to those carried out in tests to detect counterfeit components. In counterfeit detection, when a part fails an electrical test it will be set aside to be opened to determine the cause of that failure, whereas in situations of long-term storage it will be returned to the manufacturer for analysis.
The goal is have as much information as possible about the component batches stored, through testing, but also through information from the manufacturer. Once the components are in storage, periodic testing will be carried out to ensure that the components have suffered no degradation.
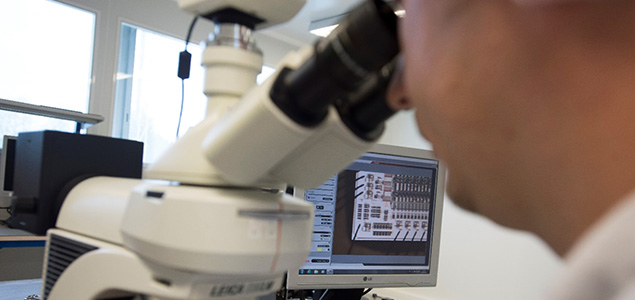
Stock management, best practices
The sizing of stocks is crucial. It is described in the UTE C96029-1 guide. It depends on the use of the component in the board’s manufacturing programme, but also on the board’s manufacturing yield and on the expected consumption for maintaining the manufactured equipment in operational condition.
The stock is separated into several batches that are stored in different locations to limit the risk of accidental destruction. Traceability to the storage location must be ensured in order to check that environmental conditions are respected and that the criteria for separation of storage locations is met.
When delivery is called for, care should be taken to choose the storage location with the highest quantity, but care should also be taken to rotate the manufacturer’s different batches regularly. The FIFO rule should be overlooked and the batches should be rotated as much as possible, the aim is to avoid being left with a single batch of components, which would be catastrophic in the event that the batch should prove to be defective.
Inventories should done regularly, without being excessive in number. An inventory entails handling of parts, and therefore increases the risk of mishandling. Ideally, parts should be managed in the form of a remote stock for the user, with a comparison at each stock movement between the computerised state at the user’s premises and that at the stockist’s premises, with an annual inventory to confirm the quantities.
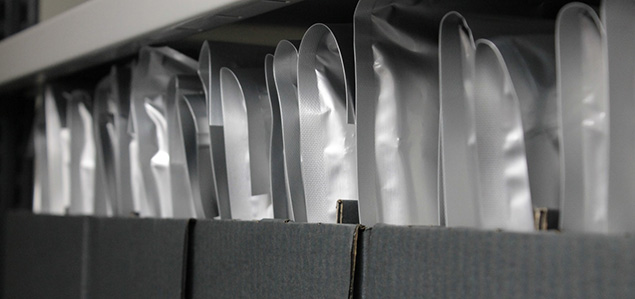
Contact
Offers tailored to the different stages of your project
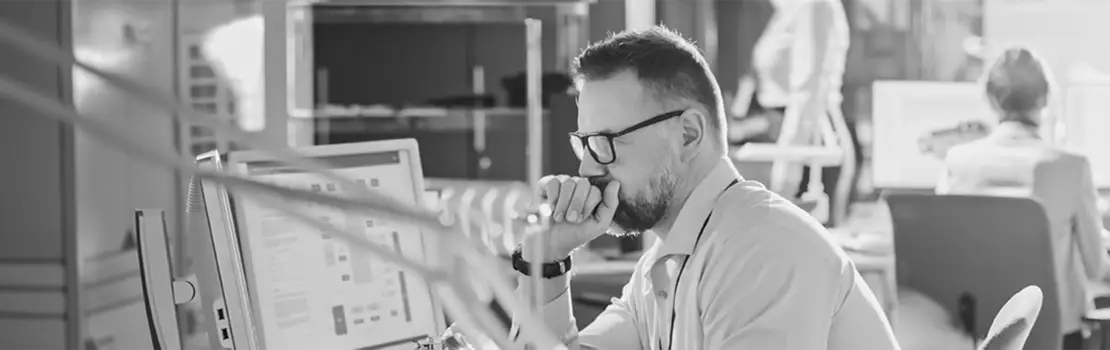
DevSolutions
Electronic product design consulting
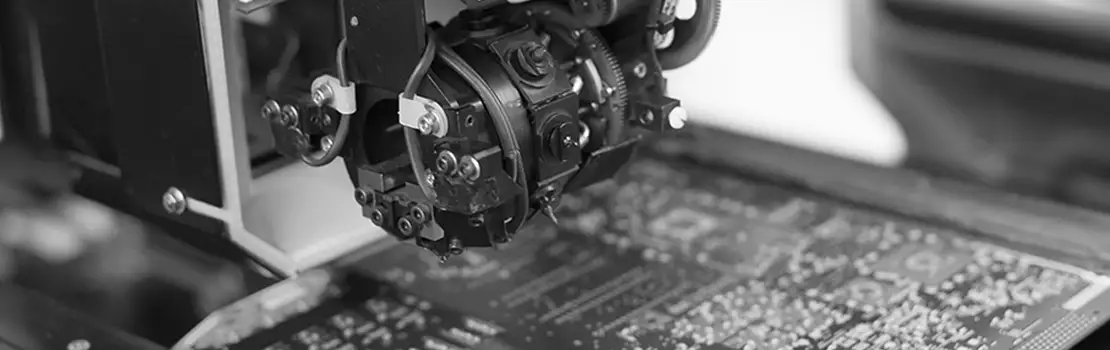
FabSolutions
Electronic component quality control
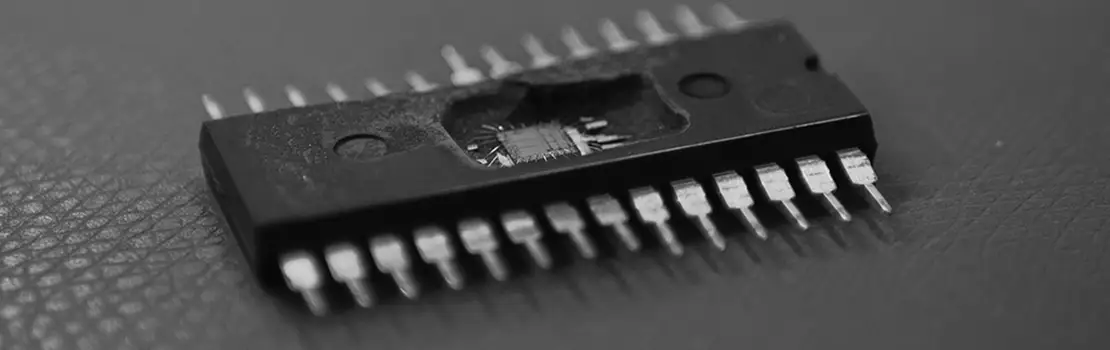
ObSolutions
Electronic component obsolescence – Advice and strategic choices